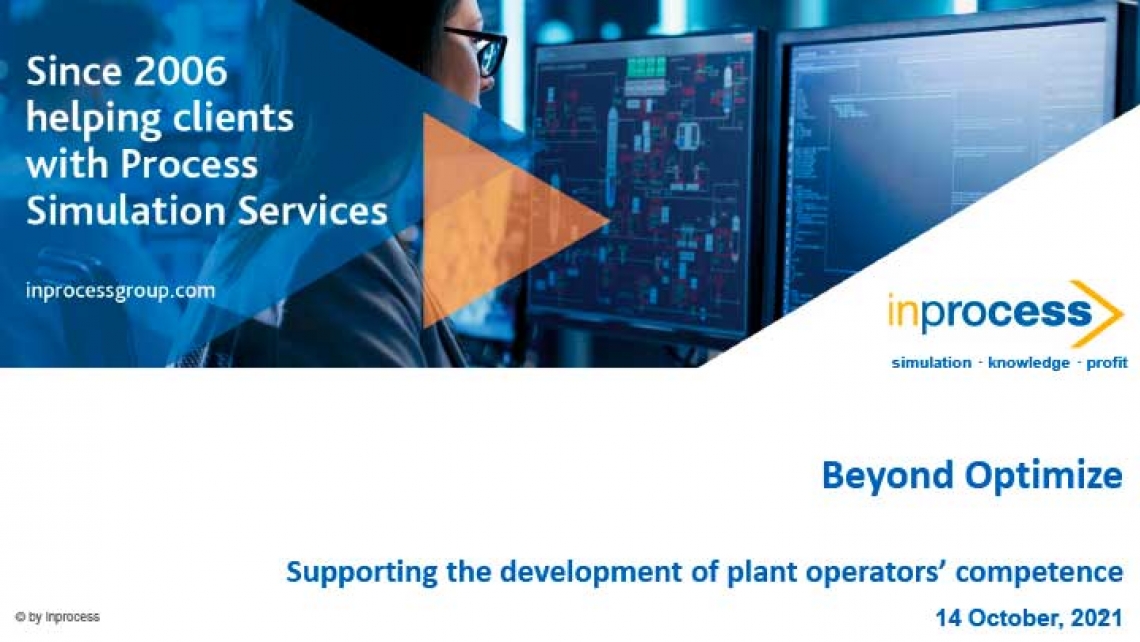
Inprocess participation in Beyond Optimize 2021: Development of Plant Operator Competence Training for a Chemistry Batch Processing Plant
Challenge
One of the main challenges that production sites face is to keep the know-how and maintain standard operations that ensure the quality of the products as well as the efficiency of the processes.
Inprocess was requested to develop a learning platform for the Spanish production site of a UK-based specialty chemicals company, Croda International, to train the operators for several fine chemistry batch processes. Among others, the needs to be solved were:
- Multi-product batch plant: huge diversity of products that can be done, lots of different steps, recipes, etc. for each one. The production needs change weekly, so operators shall have the right skills and be prepared to carry out the required actions also depending on the shift they are assigned to.
- Non-standardized operational procedures and environmental concerns
- Key senior personnel close to retire. New bunch of unskilled operators just hired
- Existing training material from different origins, timeframe, language, deepness
- HR department to implement a unified learning platform that could standardize not only the working procedures, for every product and every batch, but the way operators would learn how to apply them in their daily activities
- Encapsulate the existing knowledge and know-how of senior personnel in a corporate learning environment
Inprocess solution
Inprocess developed a customized Learning Platform ICOM (Inprocess Operator Management System) that included an emulated Operator Training Simulator (OTS) for fine chemistry batch processes.
The OTS was made part of the training platform to facilitate its accessibility from a single access point. The learning platform helped train Croda’s plant operator in terms of both time and content, focusing on the main topics they needed to learn according to their job requirements, primarily skills, current knowledge, aptitude and Croda’s production needs.
Benefits
The training positively contributed to troubleshooting daily issues and timely report to management. The benefits of the training system also extended to operations managers and human resources as they tried to fill gaps to avoid the loss of years of knowledge when experienced personnel retire as well as when they plan weekly production schedules and organize the operator shifts.
- Trainings created on a production basis schedule achieving higher flexibility
- 5 Shifts: 70 operators have already used the platform A relevant decrease of human error incidents and flaring
- 8 new learning paths created and uploaded. New training material created
- Homogeneous and centralized repository: old training material and documentation organized in the platform
- Learning paths can be tailored according to operator past experience or specific production needs to maximize the efficiency in plant.
- The learning platform can be accessed whenever is needed in the plant, hence a higher flexibility for training is achieved.
- Added to that, since the learning platform is user friendly and the learning paths are guided, the training can be done when required by the operator itself.
- The learning platform can be configured and modified with Administrator privileges; hence, HR or Management have full control of the operator learning path development as well as the capability of including new training material from any source (documents, video, presentations…) at any time.
Such a contribution is already available for downloading from our website here.
For more information, please do not hesitate to get in contact with us