Process Digital Twins
Base your operating decisions on rigorous simulation results, either online or offline.
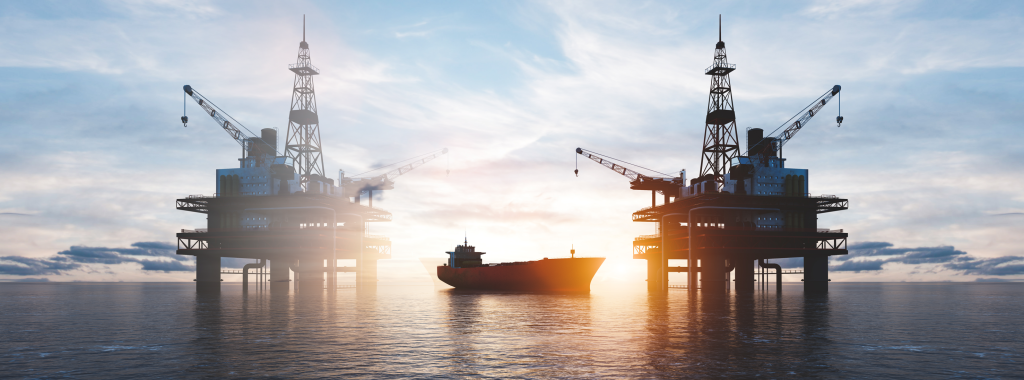
In the Process Industries, the digital twin will be the digital version of your producing asset, that contains, embedded in a high-fidelity dynamic process simulation, all the process layout and streams conditions (Compositions, pressures, temperatures, flowrates, etc.); all geometrical data of the plant equipment (sizes, elevations, sensors locations, etc.); all performance data, according to equipment provider (pump curves, compressor curves, heat exchangers rating data etc.); all actuated valves (sizing, characteristics, pressure drop, etc.); all instrumentation information (control loops, PID algorithms, instrument ranges, tuning constants etc.).
A Digital Twin can be used offline for engineering studies: to perform dynamic analysis for new process (or equipment) design & sizing; for flare systems analysis; for flow assurance analysis or for process debottlenecking studies; for control studies to evaluate alternative loop configurations, to verify the accuracy of inferred values, or to prototype APC controllers; for HAZOP or other similar PHA techniques, providing answers to many of the casuistic checked during Process Hazards Analysis sessions, reducing significantly the time devoted to them; for alarm rationalization as a supporting tool to validate the event tree even before the start-up; for operational studies to analyze the impact of other feedstocks, replicate plant issues, study new operating procedures or find ways to increase plant profitability; for Operator Training, through the addition of replicas of the Operator Consoles and DCS soft-controllers, Digital Twins are converted to a full Direct-Connect OTS.
A Digital Twin can be used online as soft sensors, calculating pressures, temperatures, flows and compositions for every stream in the plant or for every tray in a column. This data can be used by APC controllers or Operators, or back-ups of online analyzers; for bad actors detection because most of the DCS alarms look just one physical instrument. With Digital Twins, more advanced alarms can be created such as “HeatExchanger HX-001 is violating the energy balance” or “Compressor C-001 degraded efficiency”; for look-ahead predictions because Digital Twins can run faster than real time to forecast short-term anomalies or undesired conditions, for example: “Colum T-001 will start flooding in 10 min” or “Quality will go off-spec in 30 min”; as what-if advice because Digital Twins are always at the current plant state and therefore can be used by Operators and Engineers to consult about a possible action before taking the action in the real plant; for post-incident analysis because Digital Twins autosave every X minutes and it is possible to restore the plant conditions at any time. This allows deeper analysis of incidents and the possibility to repeat the incident to study the best operator action and communicate it to staff.
Services
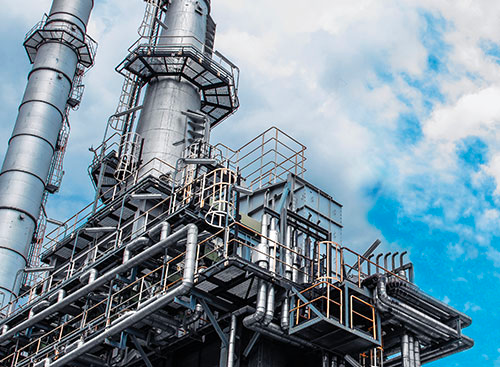
Steady State Simulation Studies
Base your decisions on high-fidelity models
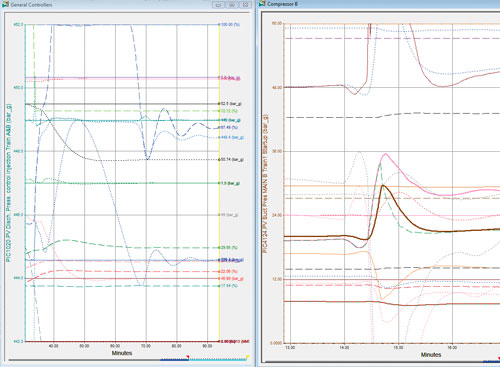
Dynamic Simulation Studies
The use of dynamic process simulation has been established in recent years as a reliable and effective tool to analyse the transient behaviour of process systems. Common examples for applications are.
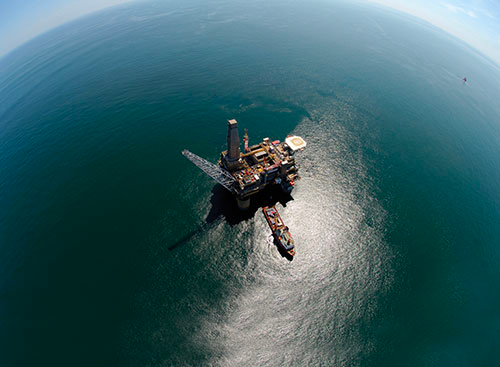
Flow Assurance Studies
By using dynamic pipeline simulation, Inprocess engineers can determine Static Hydraulic Effects in pipelines and their transient behaviour of them during upset conditions
Flow Assurance Analysis is a critical activity on field development at different project phase, from conceptual studies stages up to detailed designs.
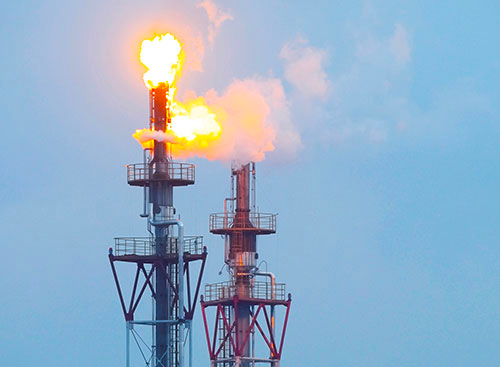
Integrated Flare Systems Analysis
The flare systems of processing plants in the Oil and Gas Industry are constantly under examination: when new plants are built and connected to an existing flare header, when existing plants are extended, or when new regulations have to be applied to an existing system. Often dynamic analysis of the flare system or the flare gas sources can bring relief to bottlenecked flare systems. Nevertheless, in order to apply such dynamic analysis and get dependable results, one needs significant expertise.