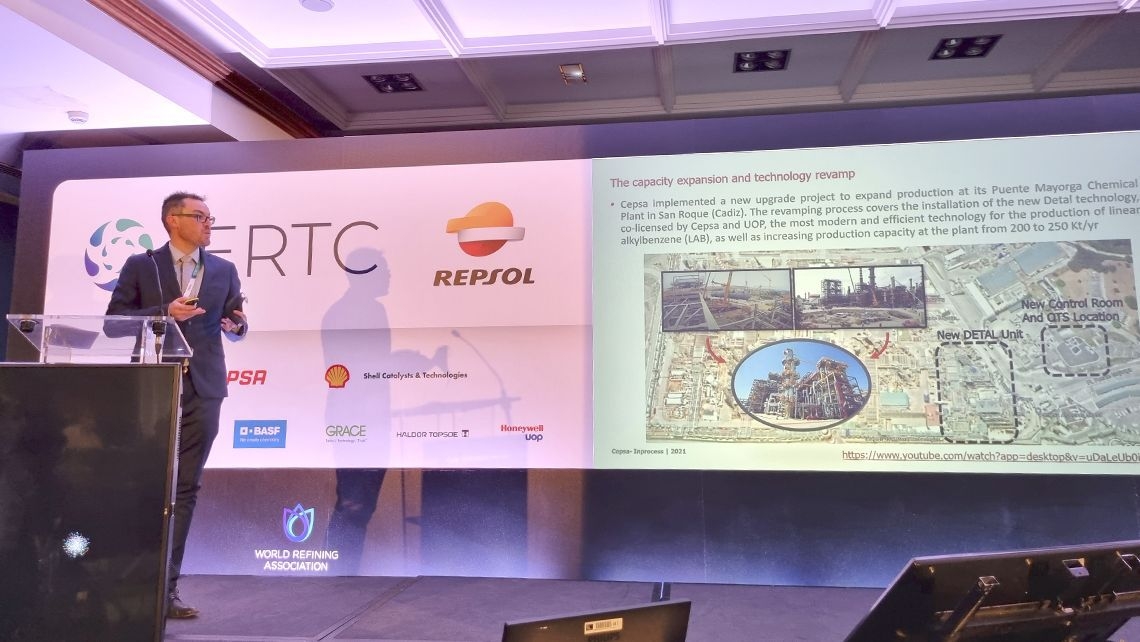
Inprocess contributes to ERTC 2021
Since its inception in 1995, the European Refining Technology Conference (ERTC) annual meeting is the leading event of the year for the global oil refining industry. This edition has taken place in Madrid from 15th to 18th November.
One of the most attractive features at ERTC are the presentations, that offer attendees high level market insights, project updates, best practices and case studies, as well as the latest in process and technology developments.
In the case of Inprocess, our experts Chemical Engineering Ph.D. Miguel Angel Navarro and Daniel Martínez, Sales Director, together with Daniel Salvador García, Process Engineer at CEPSA have given a presentation based on a successful project: “Benefits of Digitals Twins and VR for greenfield projects”.
CEPSA contracted Inprocess to develop an Operator Training System (OTS) based on a rigorous dynamic process simulation model for a revamped plant. The key point to be addressed was the process to be modelled: Linear Alkyl Benzene (LAB) that is used for detergents.
The old production plant was substituted for a new one using a newly developed technology: the more sustainable and environmentally friendly Detal process. The process is a fundamental part of operator training and Detal is a complex process with different phases, therefore a major focus of the project.
The main challenges for the OTS in this case involved:
- The proper selection of the process simulator which includes the necessary characteristics to this OTS.
- Ensure that OTS provides a real experience during the operators training. Look for strategies to ensure a real time simulation speed in very big simulation models
- Implement alternatives creative solutions to solve technical problem related with the simulation of the plant process (e.g., the adsorption process as Operation Unit is not include directly in Aspen Hysys).
- The emulated OTS included a large number of pieces (simulation models, emulated ICSS, graphic interface, 3DVR models, different instructor/operator stations…) that has to be interconnected synchronously. The communication is done though IIS (Inprocess Infraestructure Suite).
After the development of the Digital Twin by Inprocess based on a rigorous dynamic process simulation model of the new plant, which is also connected to a detailed 3D Virtual Reality model of the plant, the main benefits obtained are the following:
- The full operations team can practice critical events such as startups, shutdowns and emergency responses in a fully realistic manner resulting in improved safety, enhanced efficiency and reduction of emissions in the plant.
- Increased operability thanks to the use of 3DVR to train control and field operators and the use of AI together with the design “Best field practices”.
- Safer, shorter and smoother plant start-up.
Such a contribution is already available for downloading from our website here.
For more information, please do not hesitate to get in contact with us.