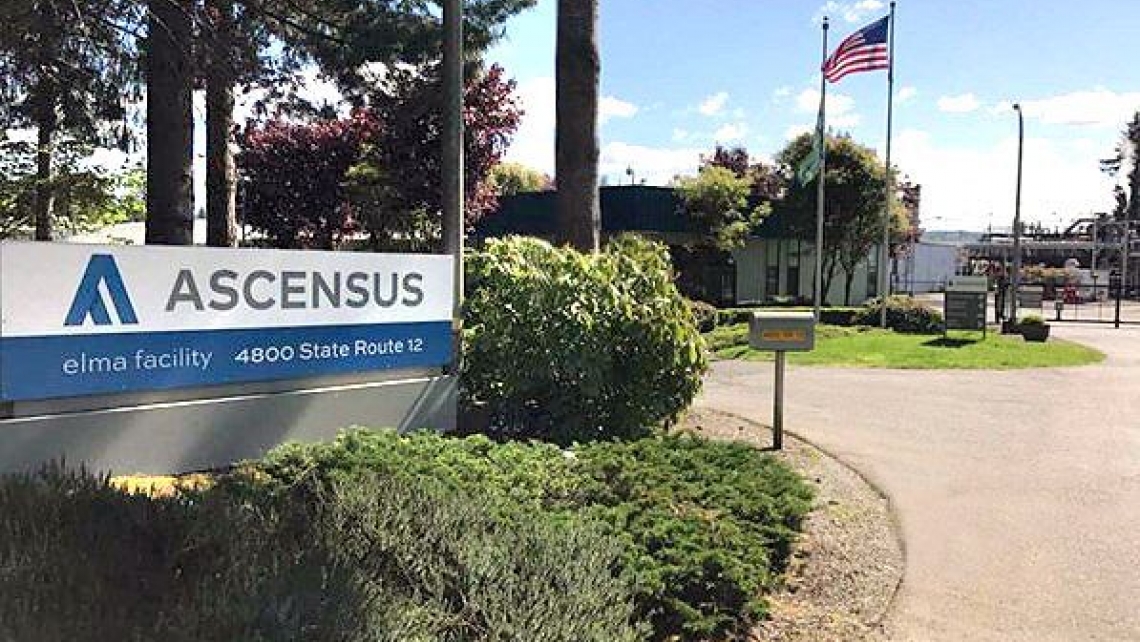
Inprocess develops a Direct-Connect Operator Training System for Ascensus Specialties Hydrogen Plant in Elma, WA (USA)
Inprocess, a process simulation services and consulting company, has been awarded to provide Direct-Connect Operator Training Simulation system for Ascensus Specialties Hydrogen production plant in Elma, WA.
Inprocess has been awarded the development of an Operator Training Simulator (OTS) for Ascensus Specialties’ hydrogen production plant at their world-class production plant in Elma, Washington that provides the growing, global demand for high-quality Sodium Borohydride, reactive and alkali metals, boranes, and related chemical compounds.
The project includes the design, engineering, delivery, testing and installation of the OTS at site, including the development of training scenarios. For the execution of this project, Inprocess will use Aspen HYSYS® Dynamics as the process simulation engine, Emerson’s SimulatePro as the DCS emulation package, and Inprocess Infrastructure Suite (IIS) to provide the OTS backbone for data connectivity, instructor functions and trainee evaluation.
This Direct-Connect OTS by Inprocess utilizes a high-fidelity dynamic model of the process, including the following plant areas: Natural Gas Preparation, Catalytic Reformation furnace, Catalytic Shift conversion, PSA, Vent Gas Recovery, Waste Heat Recovery/Steam Generation, and Water Treatment.
The OTS will allow for plant operations to reduce the amount of time to certify operators by providing a simulated environment to operate the plant on scenarios without the need to shutdown or put the operating plant at risk. The OTS will train the operation staff on the process and the control system, reduce the risk of major operational incidents and increase plant on-stream time and performance. Additionally, by using the process simulation package that the Ascensus engineering team uses internally, the OTS provides a test-bed system for engineering analysis and testing of changes prior to implementation. Once delivered, this Operator Training Simulator will provide the hydrogen plant operations with:
- Reduced cost and time to certify operators
- Increased operator competency
- Reduced downtime
- Increased plant safety and uptime through increased operator experience of the plant processes and development of diagnostic skills that increases recognition and improved responses to emergency and/or upset situations
- Better awareness of the process behavior
- Training on long-term system responses and/or complex sequences of events
- An engineering and operational testing system
The Operator Training Simulator will also provide the process engineers and the process control engineers at site to study planned plant modifications in the process scheme / design or process control scheme.
Project has already started and is planned to be delivered at the end of Q1 2022.